Plastics labs are commonly tasked with testing a high volume of similar specimens while trying to maintain consistent, reliable results. Some can manage the challenge with a largely manual, human-run operation, but most companies will greatly benefit from automating at least some of their testing equipment.
Incorporating automation into existing testing processes can benefit plastics manufacturers by offering:
- More repeatable results
- Higher throughput
- Better (and safer) use of labor
- More secure test data
The extent of those benefits may vary among different manufacturers, but most labs can expect to see significant ROI from taking steps to automate.
Enhanced RepeatabilityFor plastics labs that test hundreds of similar specimens each day, repeatability is typically a big concern — and a challenge. Adherence to strict testing standards such as ASTM D638 or ISO 527 requires consistent results that can be difficult to achieve when the potential for human error is prevalent.
Many plastics standards are quite complicated and require "very, very precise" measurements such as modulus, said Instron applications engineer Sammi Sadler.
Variations in technique from one operator to the next — or even variations by a single operator — can result in less consistent, less reliable test data. A human user may not always be able to load a specimen perfectly vertically, for example — and any such difference in the angle can influence results.
The biggest variables in plastics testing stem from alignment, measurement, and grip pressure, said Sadler.
"If we're thinking about screw side action grips to test plastics, the amount of pressure that they apply when clamping onto the specimen — that pressure could vary from specimen to specimen, or from user to user," she said.
An automated setup tackles this problem by ensuring that the measurement, insertion, and alignment of every specimen is done the same way — offering great potential to save the time and expense involved with discarding failed specimens.
Armed with more consistent data that is not affected by human errors or variations, lab operators can more easily analyze results, said Kelvin Fernandez, Instron's upstream marketing manager for robotics systems.
"You can say, 'I know I've cut this variable out, and my results are still bad' — so it's product related, or maybe test setup related or something like that," said Fernandez.
Better Throughput — Without Adding StaffWith the sizable quantity of very similar specimens tested, plastics labs can improve efficiency and throughput significantly by automating at least some of their processes, said Instron automation specialist Richard Spiegel.
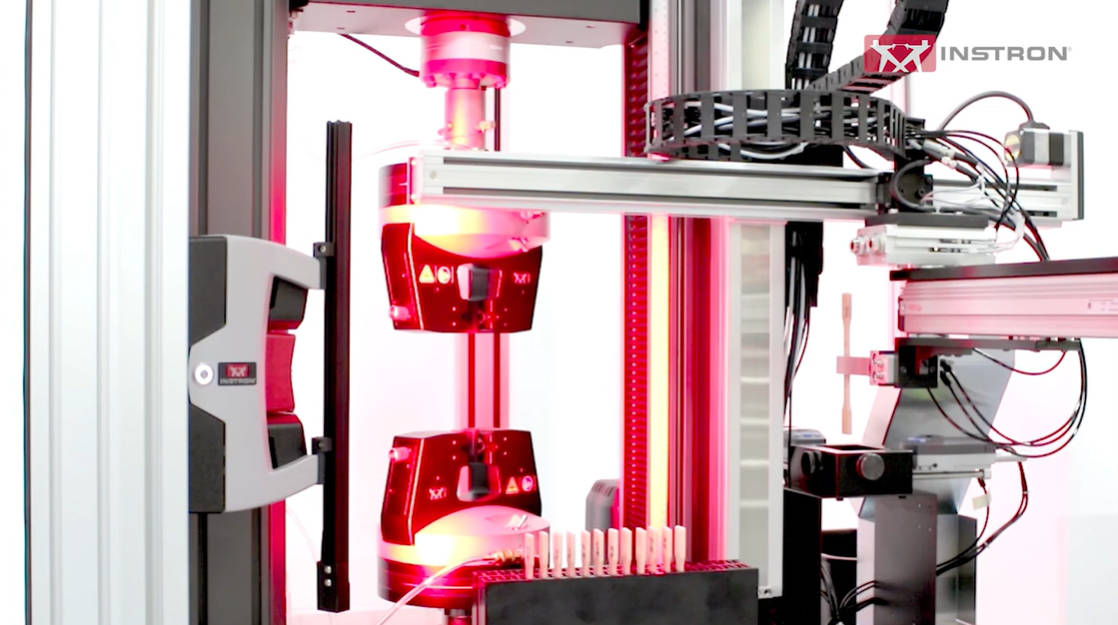
"It's the same over and over again," he said. "Automation just becomes that much easier, and when it's easier, it becomes that much cheaper."
When a system can load enough specimens to run unattended tests overnight, the lab can expand its throughput without staffing another shift — and see cost savings that help compensate for the up-front expense of implementing automation.
Optimized LaborThe greater the level of automation, the more tasks a human operator can manage when they do not have to closely monitor the test frame. As the automated sequence runs, they can analyze data or prepare the next round of specimens — or if they have other test types that still require a manual process, they can conduct those tests on another system.
Some companies look to automate almost out of necessity because they simply cannot find qualified applicants to fill open lab positions, said Spiegel.
"They don't have someone there to load the test frame anymore," he said. "They're trying to fill a position like that and they're struggling, so they really need to make much better use of the labor that they do have."
Sadler agreed that staff turnover in testing labs can play a role in the decision to automate.
"It's really frustrating to bring people up to speed on how to test to meet these standards," she said, "so being able to not worry about turnover also adds to the benefit of automation."
Health and SafetyFor human operators who work in the plastics lab, an automated testing system like the AT3 or AT6 spares them from loading and unloading specimens repeatedly, pinching their fingers, or straining to lean at the correct angle when a test frame is not located in an ergonomically friendly position.
Instead of operators performing potentially hundreds of repetitive motions throughout the day, Spiegel said, they can test the same volume with far less physical labor. Alignment, measurement, and disposal of the specimens are handled automatically.
"They're now loading a rack into an automation system and hitting Start once," he said. "And it's doing that same amount."
Locked-Down DataProtecting testing data is just as critical as the testing process itself. Bluehill Universal test results are automatically exported into an organization's production system.
And with proper security features enabled in the software, users who do not yet have the requisite training and experience can be assigned a lower level of permissions — helping to prevent that valuable data from getting altered or deleted inadvertently. This helps to ensure repeatability — which, again, is a key challenge in plastics testing.
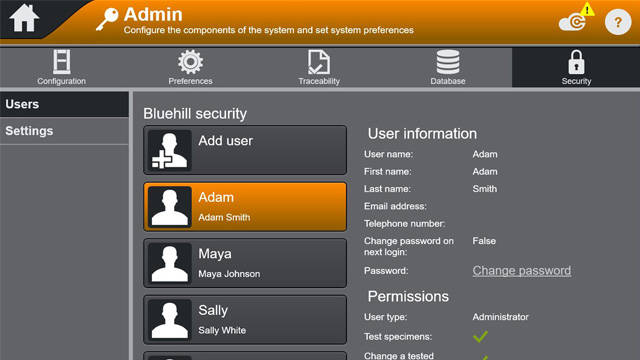
Bluehill's Traceability Module also provides a full revision history so that every addition, deletion, or modification is recorded along with a timestamp and the name of the user who made the change. Those with proper access will know what was altered, when, and by whom.
"You have a very auditable trail of any changes that have been made," said Spiegel.
And since Bluehill comes with prebuilt test methods that are specifically designed for common plastics testing standards — such as ASTM D638, ASTM D790, ISO 527, and ISO 178 — the software does much of the work for the lab.
"So they just don't have to think about it," said Sadler. "That's something that also brings comfort to the customer."
Steps Toward Greater Efficiency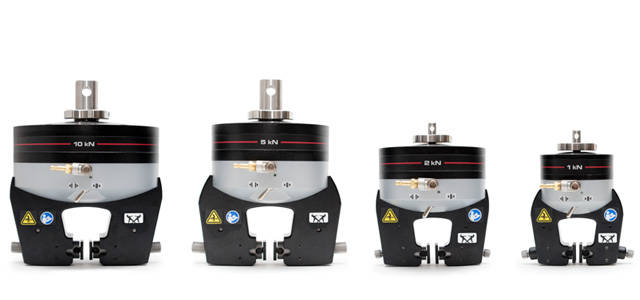
Not every manufacturer that works with plastics will be ready to adopt a fully automated testing setup, but even incremental steps can help make notable strides to enhance efficiency. Upgrading to an automatic extensometer or replacing older manual grips, for example, can translate into more consistent tests for organizations that do not want to move away from their human-centric environment.
"Going from advanced screw side action grips to pneumatic grips is a huge step toward more repeatable results," said Sadler. "And then adding more and more automated solutions is the most ideal."
Depending on the level of automation that it ultimately adopts, a lab can dramatically transform its operation — boosting its throughput, without adding more shifts, while enabling human operators to make more productive use of their time.
"Just imagine yourself for eight hours a day, sitting in front of a frame and loading, waiting for it to be done, and then removing the pieces and then reloading again," said Fernandez. "That's the main problem or the main pain point for the customer, really, is that waiting."